L'usine LEMKEN à Alpen
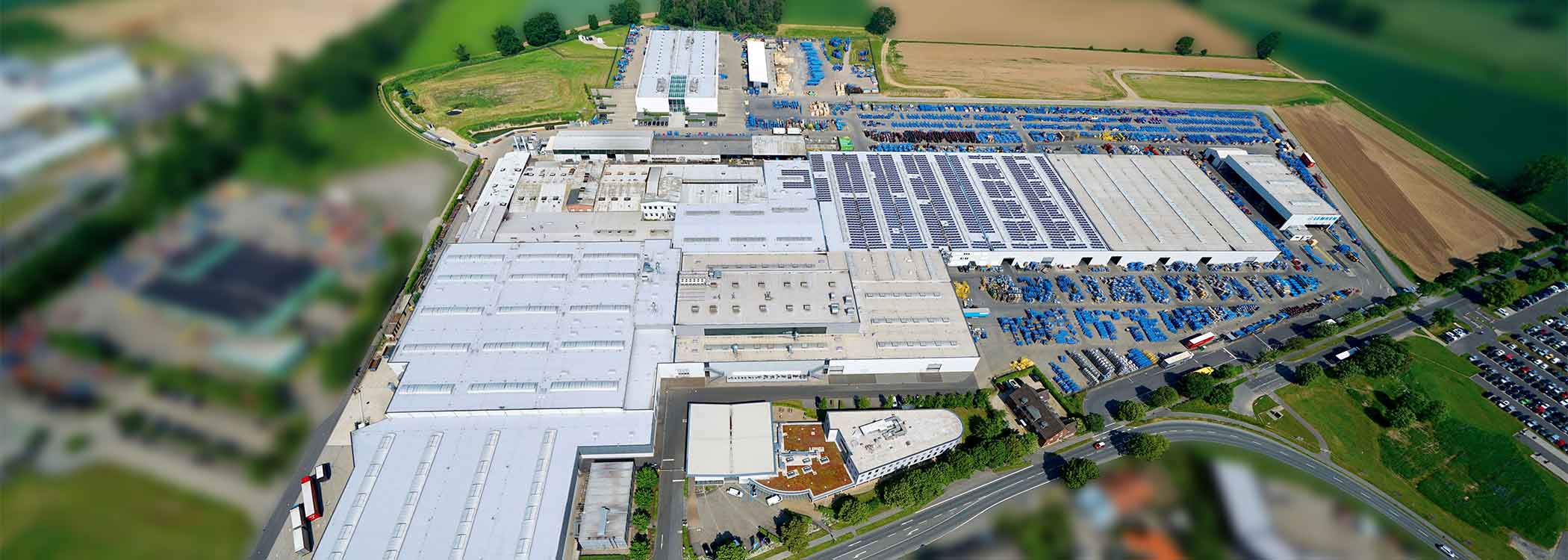
En visite à l'usine LEMKEN d'Alpen
Comment l'acier est-il transformé en une machine agricole de haute technologie? Quelles machines sont utilisées sur la chaine de fabrication et comment travaillent les employés LEMKEN?
Une visite guidée de notre usine vous permettra de suivre de près l'ensemble du processus de fabrication des machines agricoles à Alpen.
Nous aimerions partager avec vous l'intérêt des chaines de fabrication dans nos usines sophistiquées: de la mise en forme de l'acier brut dans des centres de traitement à commande numérique, aux robots de soudure et au système de revêtement par immersion cathodique.
Nous vous invitons à vous faire une idée par vous-même.
Visite virtuelle de l'usine
Ici, nous vous donnons déjà un petit aperçu de notre production à Alpen.
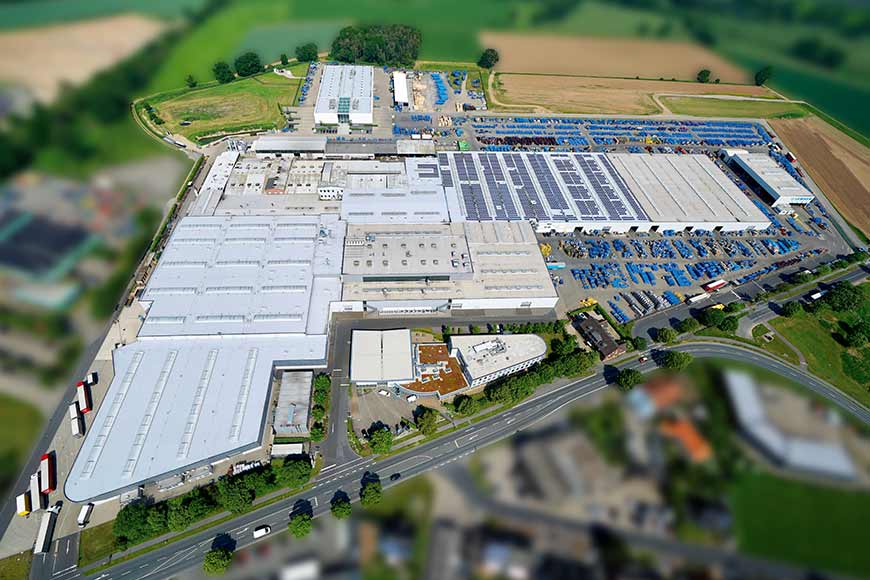
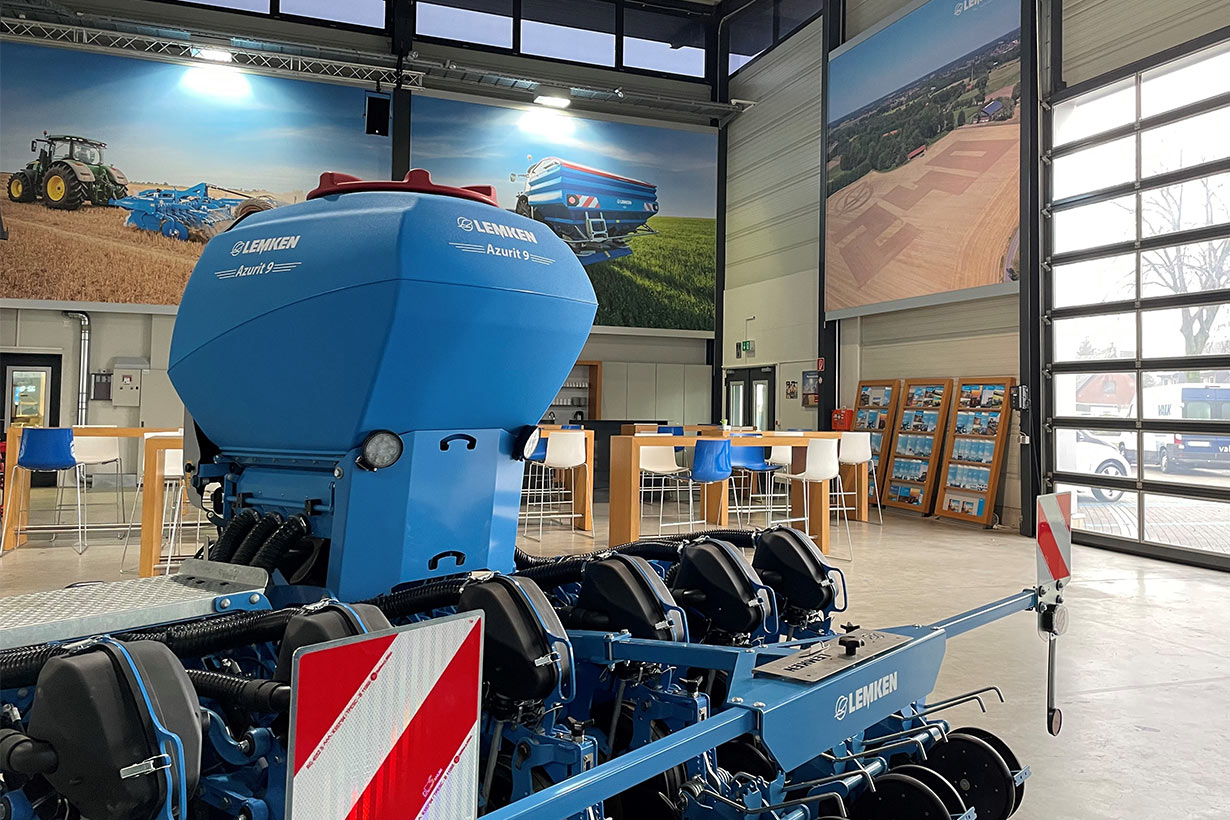
L'AgroForum, d'une superficie de 625 m2, est utilisé de manière polyvalente comme hall d'exposition, pour des présentations de machines aux clients et pour les événements les plus divers. Chaque année, nous y accueillons plus de 5.000 visiteurs du monde entier. C'est également ici que se trouve la boutique des fans de LEMKEN, avec une large gamme d'articles de merchandising. Ceux-ci peuvent également être achetés en ligne.
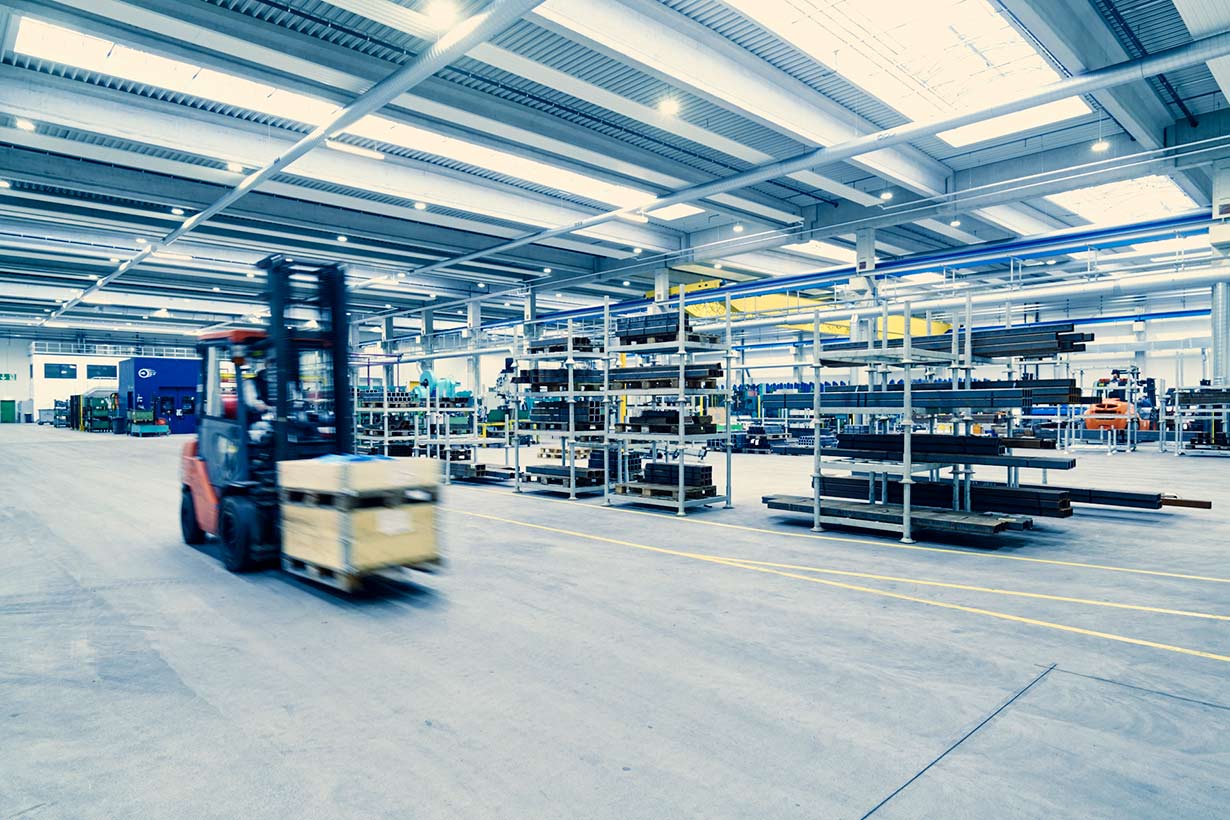
Sur une surface de 5.000 m², les pièces achetées sont déchargées, marquées et enregistrées dans le système. Elles sont soumises à un contrôle de qualité avant d'être stockées ou transportées en lots plus petits vers les lignes de montage. Dans l'entrepôt de matières premières, 1.800 à 2.000 tonnes d'acier de qualité sont transbordées chaque mois sous forme de tôles micro-traitées, de larges plats, de barres, de profilés ainsi que de tubes ronds et de profilés carrés en acier, principalement en provenance d'Europe occidentale.
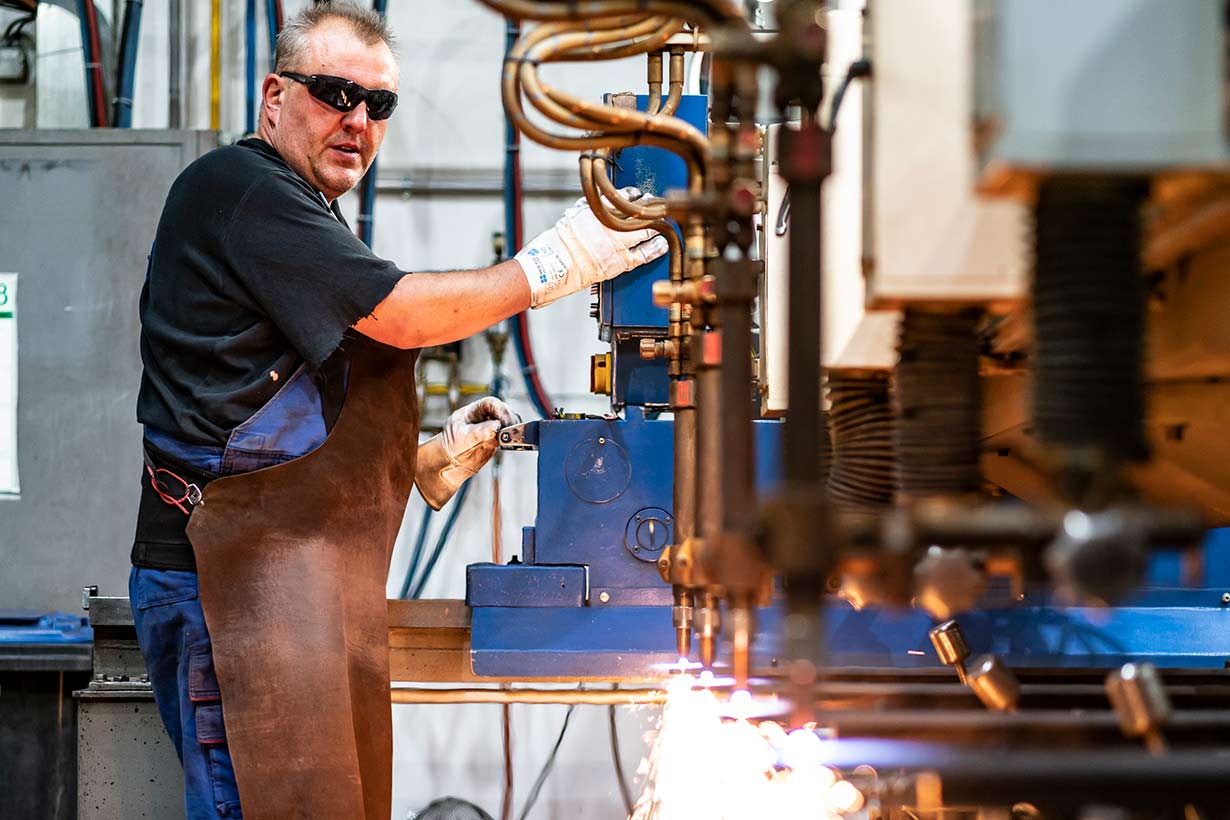
Ici, des installations de poinçonnage et de cisaillage commandées par ordinateur mettent l'acier reçu à la bonne longueur. En même temps, les perçages et les marquages sont déjà réalisés. La découpe des tôles s'effectue sur une machine d'oxycoupage et une installation d'oxycoupage à commande numérique pour les tôles d'une épaisseur maximale de 120 mm. Les pièces sont ébavurées et les bords arrondis sur une machine d'ébavurage avant l'étape de traitement suivante.
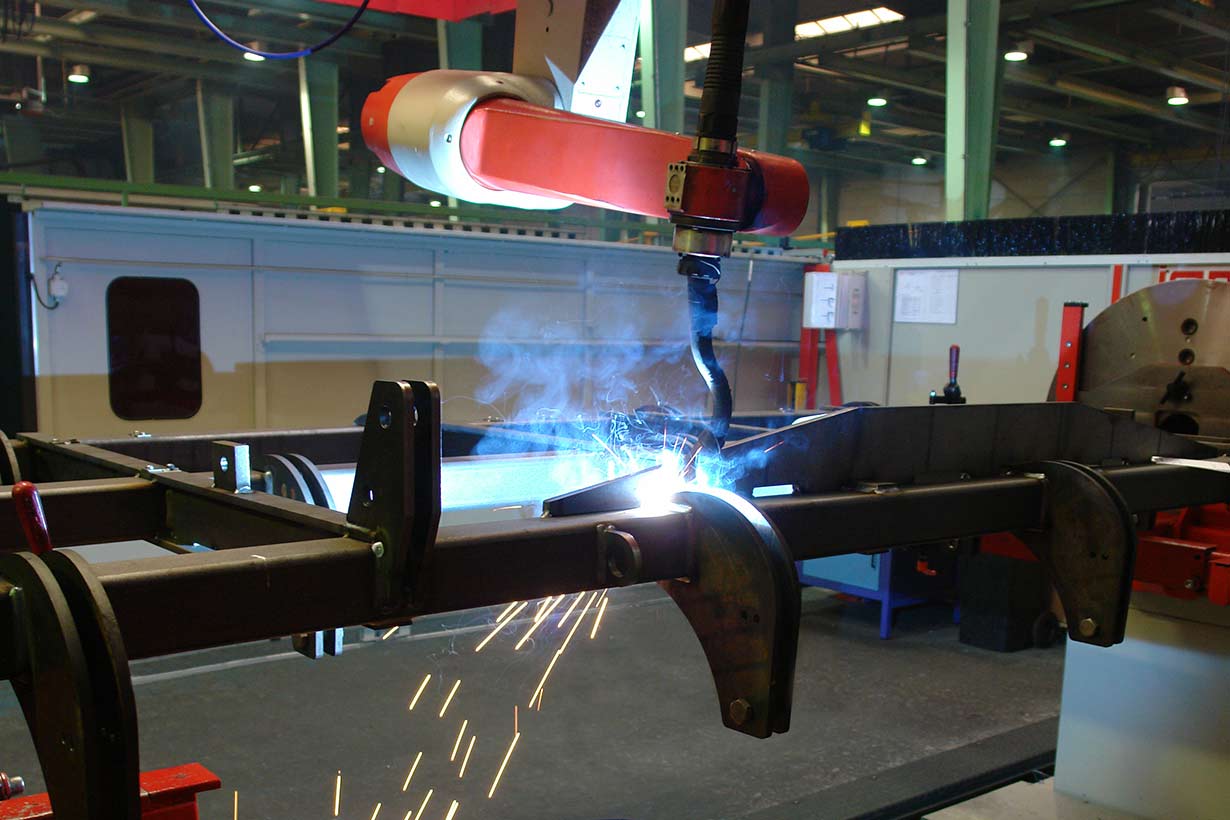
Les châssis des outils de travail du sol et les caissons des herses rotatives sont soudés par différents robots de soudage selon des consignes définies. Ce haut degré d'automatisation garantit une précision maximale et une capacité de production élevée. Quelques postes de soudage manuels complètent le travail des robots, par exemple pour les pièces surdimensionnées.
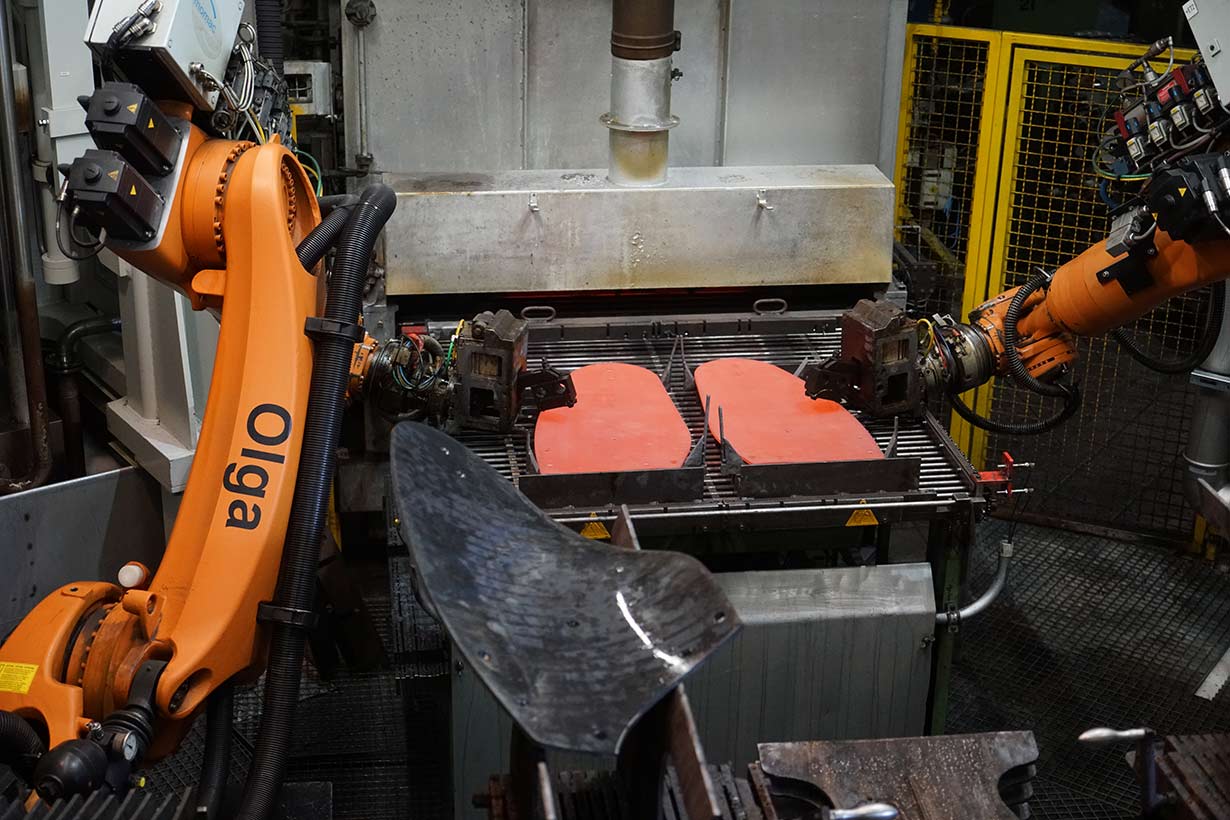
Dans le cadre d'un processus de trempe et de revenu optimal, de nombreux paramètres différents, tels que les courbes de température ou les émulsions, sont harmonisés de manière à ce que les pièces présentent exactement le rapport requis entre élasticité et dureté. En fonction des dimensions et de l'utilisation des pièces à tremper, on utilise aussi bien des fours entièrement automatisés avec commande robotisée que différents fours rotatifs et à chambre, ainsi que des fours de revenu et des presses.
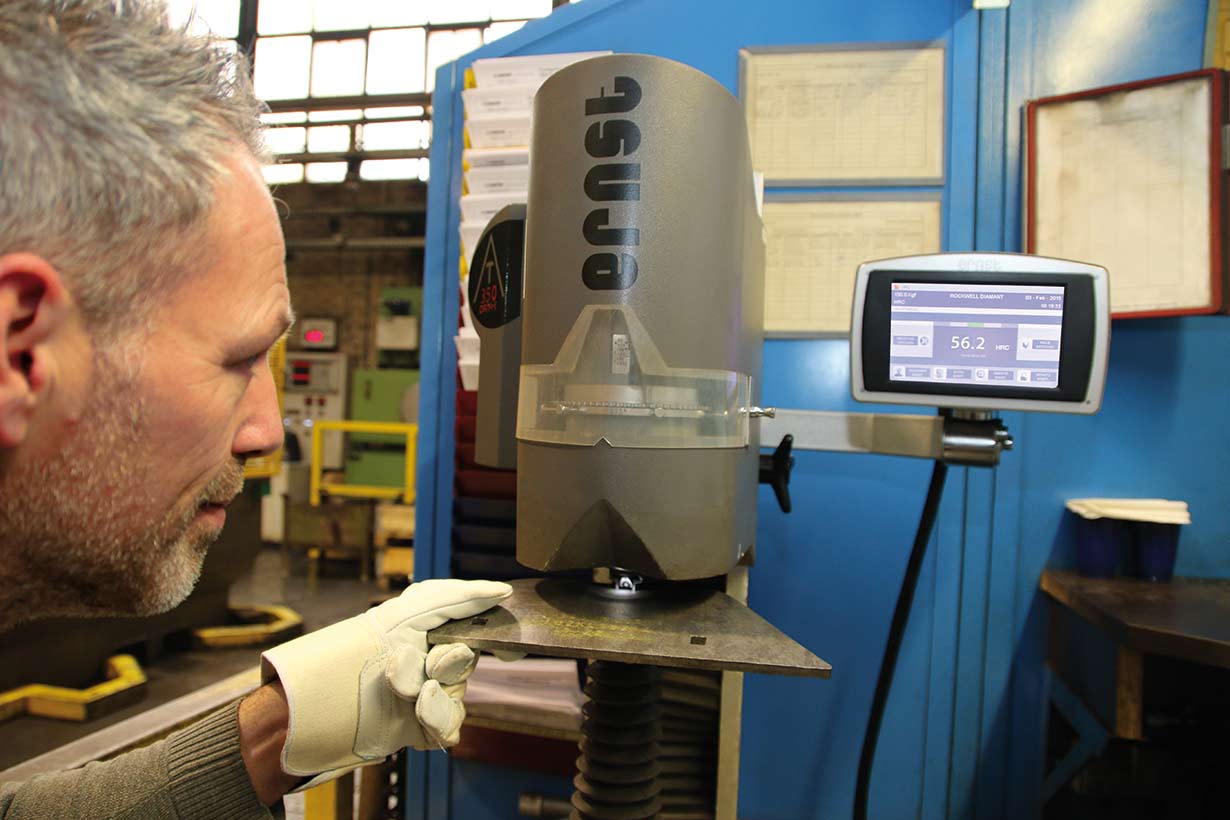
Des contrôles de qualité réguliers en laboratoire ou sur place garantissent le haut niveau de qualité des machines et des pièces. Chaque livraison d'acier entrante est contrôlée à l'aide d'un appareil d'analyse spectrale mobile afin de vérifier sa composition chimique correcte. Ainsi, l'acier qui ne répond pas aux exigences n'entre pas dans la production. La dureté et l'élasticité des pièces traitées sont contrôlées en laboratoire et la production en cours est surveillée en permanence.
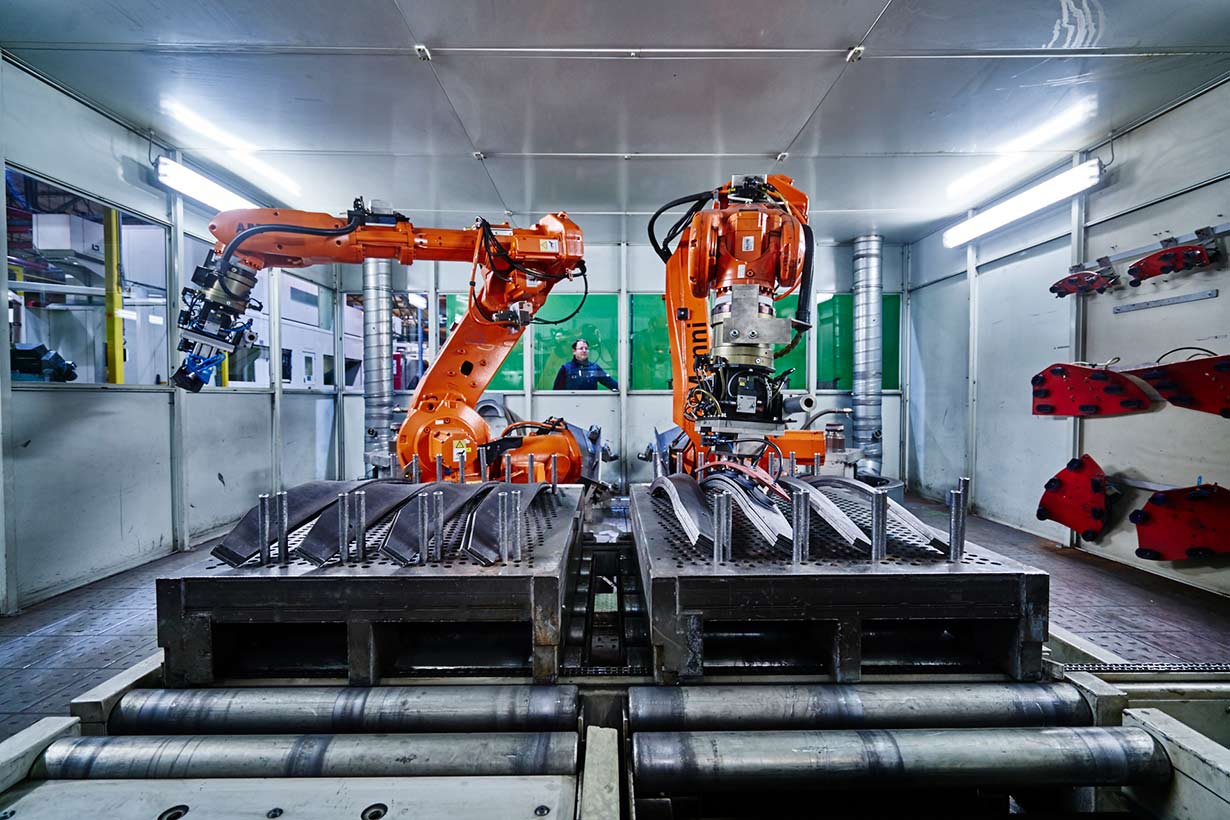
Juste avant la mise en peinture, les pièces d'usure de la charrue sont ponçé afin que la charrue soit facile à tirer et puisse travailler en économisant du carburant. Les robots de ponçage procèdent en deux étapes. Tout d'abord, ils préparent les pièces dans une position bien définie. De là, les robots prennent en charge les pièces et les font passer sur la tête de ponçage rotative. Le sens de ponçage correspond à l'écoulement de la terre sur le versoir et les arêtes restent vives.
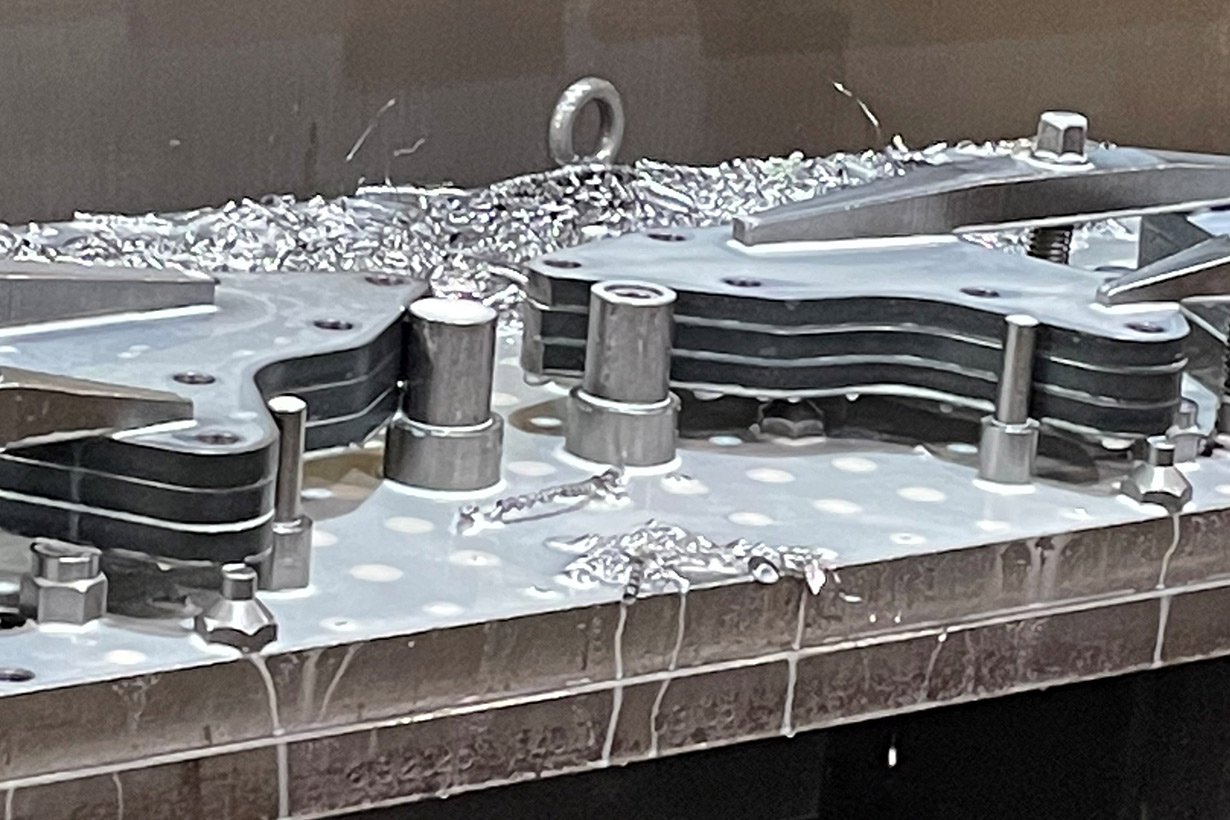
La finition par enlèvement de copeaux (perçage, tournage, fraisage) est réalisée sur 15 centres d'usinage conventionnels et à commande numérique. C'est surtout l'usinage mécanique de pièces d'usure trempées qui requiert une compétence maximale et des machines robustes. Un savoir-faire essentiel réside dans la création des dispositifs de production. Les postes de réglage d'outils situés en amont minimisent les temps de préparation et assurent l'utilisation des capacités des machines. 50 collaborateurs y travaillent en 3/8.
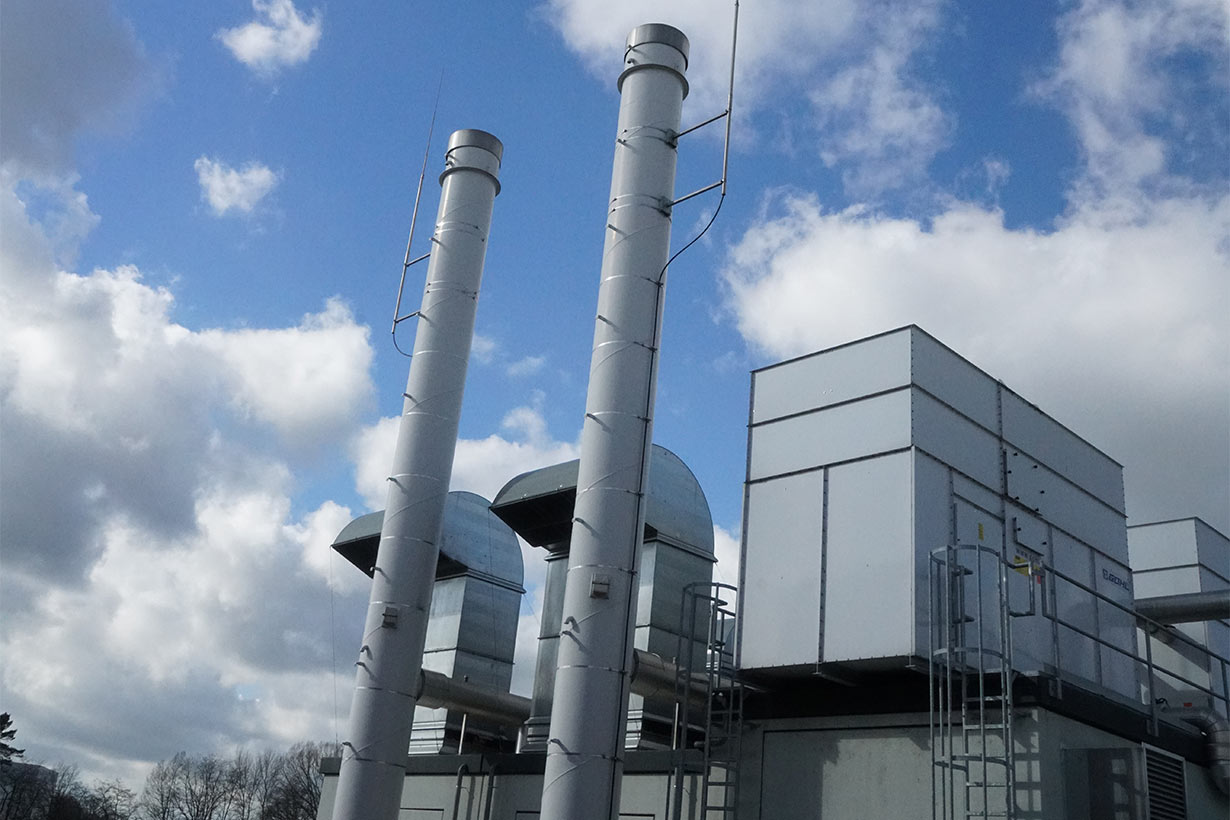
LEMKEN dispose d'un vaste système de gestion de l'énergie. La chaleur résiduelle de l'atelier de peinture est stockée et utilisée pour le chauffage. Des panneaux photovoltaïques complètent l'alimentation électrique. Deux centrales de cogénération avec machine frigorifique et réseau de chauffage urbain, d'un rendement global de près de 87 pour cent, produisent une puissance thermique et électrique de 1.800 kilowatts chacune. Elles ont également permis de réduire de 70 pour cent la consommation d'eau souterraine pour le refroidissement des bassins dans la transformation.
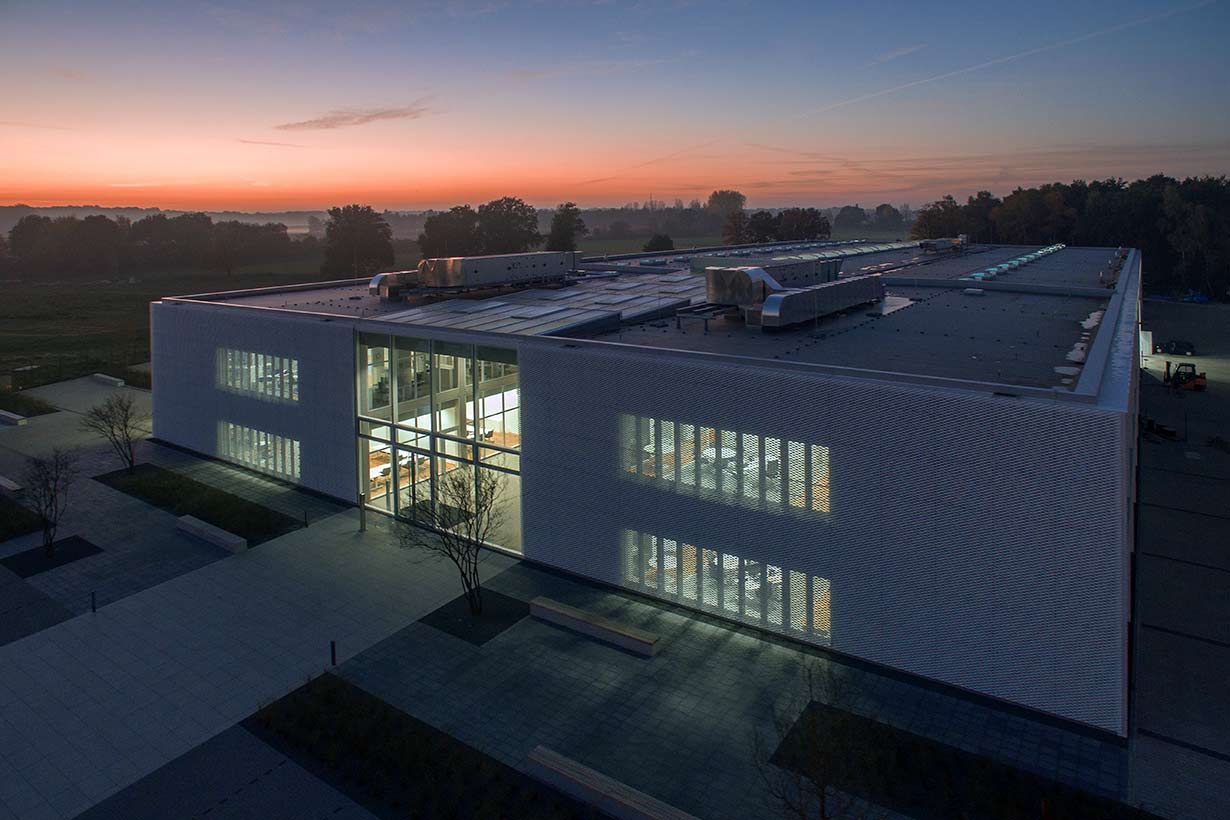
Le centre de recherche et développement a été inauguré en 2016 et comprend, sur une superficie de 5.800 m2, un hall d'essai de 4.200 m2 avec un laboratoire et des installations de simulation. 3.100 m2 de bureaux ouverts et transparents sur deux étages offrent des conditions de travail optimales pour 143 ingénieurs et techniciens. Le bâtiment est conçu pour être économe en énergie et est entièrement chauffé par sa propre centrale de cogénération.
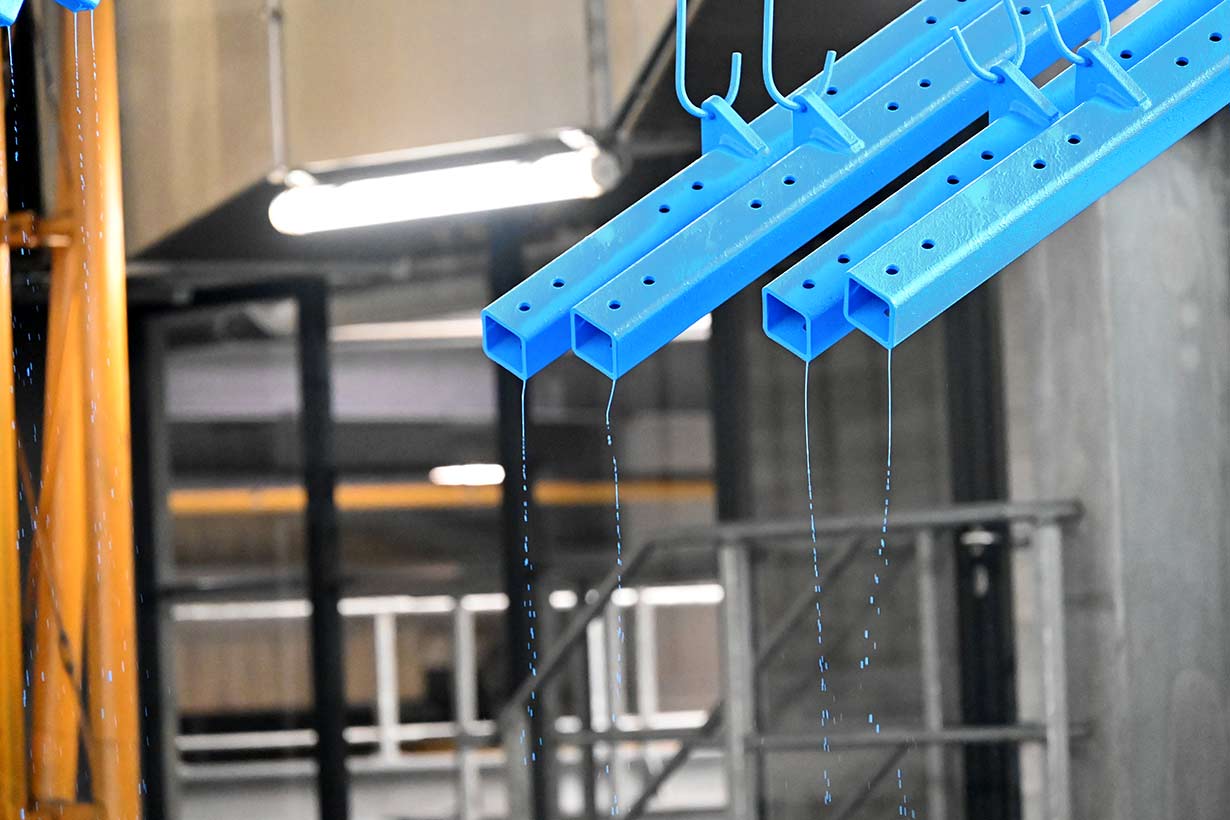
Les composants des machines sont peints avant d'être assemblés. Pour ce faire, ils sont suspendus dans des traverses et passent d'abord par deux grenailleuses pour le nettoyage mécanique dans un système de rails. S'ensuit le processus de nettoyage et de peinture entièrement automatisé dans les 13 cuves d'immersion successives de la peinture par immersion cathodique, avant que la peinture ne soit conservée dans un four de cuisson. La distance totale de convoyage est de 1,1 km.
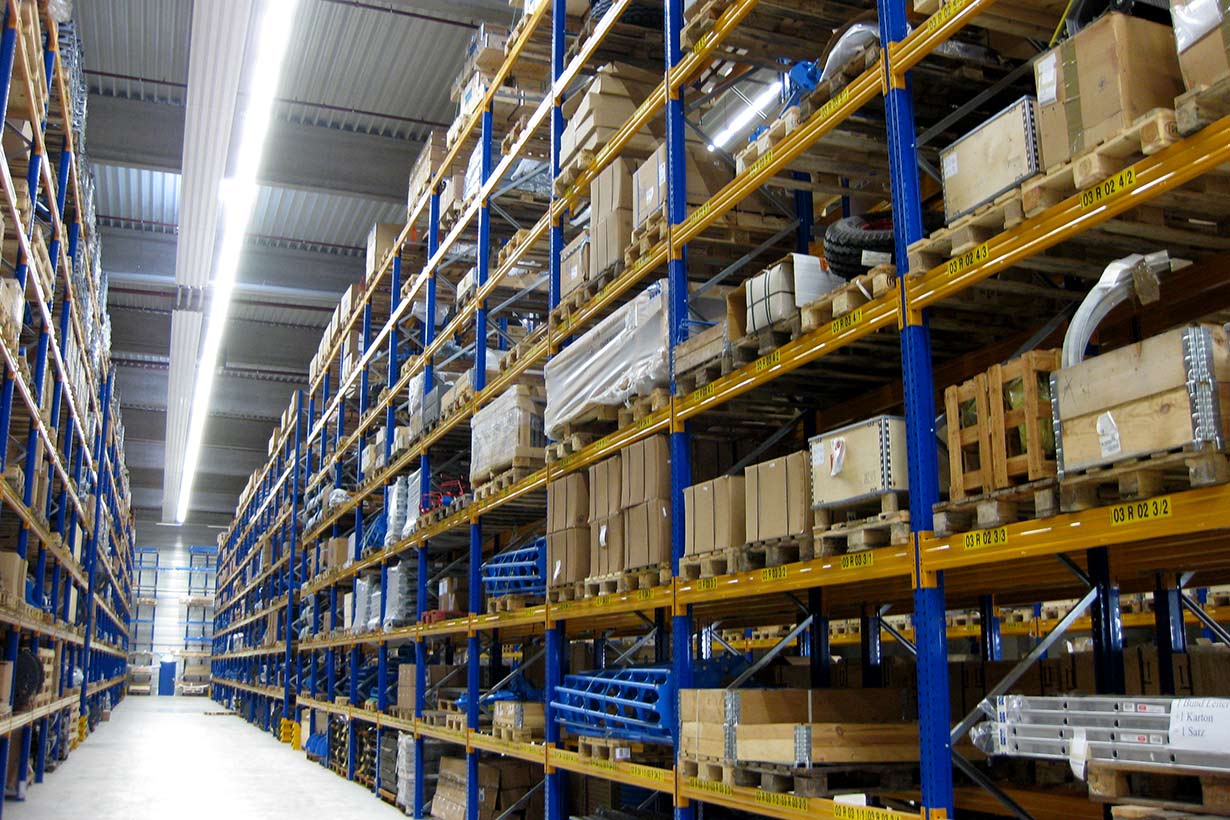
La logistique des pièces de rechange a été externalisée dès 2001 auprès d'un spécialiste. Les pièces de rechange sont livrées deux fois par jour par navette au centre logistique Imperial, situé à 60 km, d'où elles sont centralisées pour être expédiées dans le monde entier. Chaque année, jusqu'à 70.000 ordres d'expédition sont envoyés, représentant 370.000 positions et 8 millions de pièces détachées.
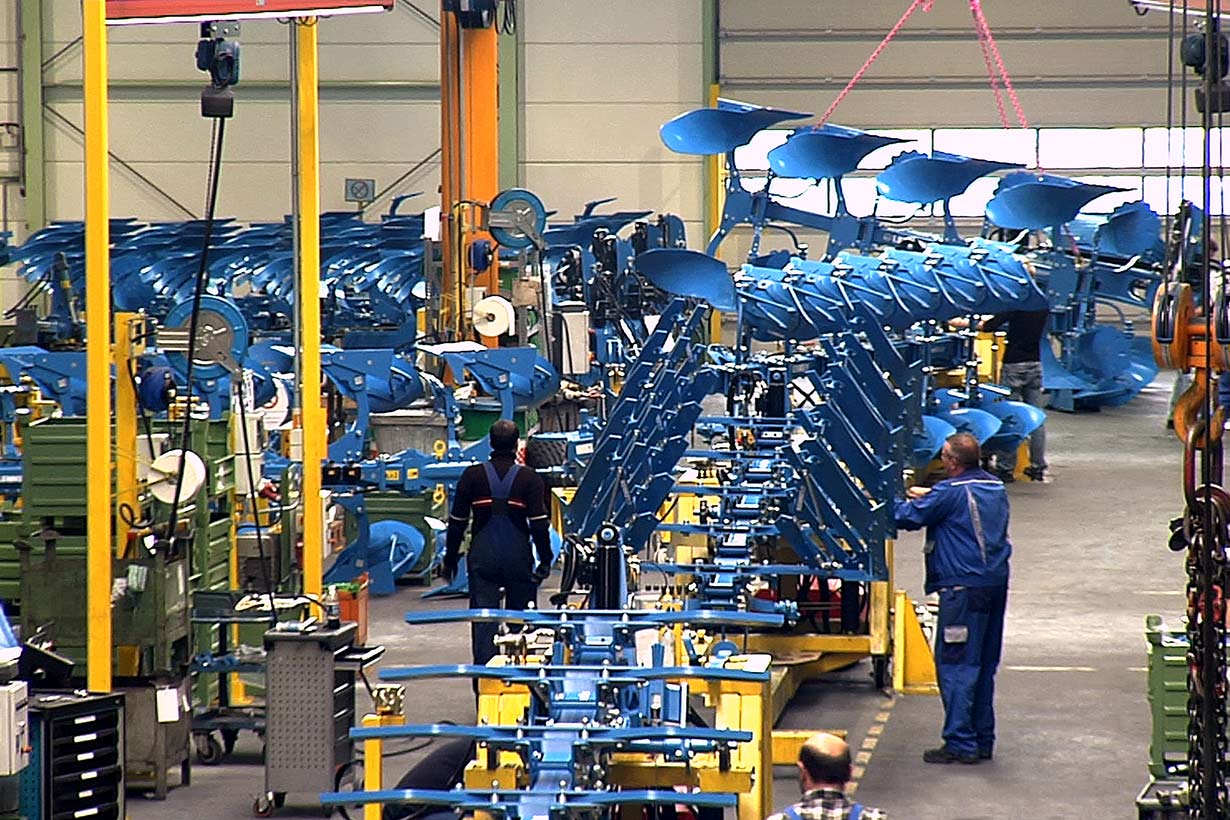
Dans les 3 halls de montage, tous les outils de travail du sol LEMKEN sont montés individuellement dans les lignes de montage respectives, selon les commandes des clients : Charrues, cultivateurs, déchaumeurs à disques courts, herses rotatives et combinaisons de lits de semences. Le montage final est souvent précédé d'un prémontage de certains sous-ensembles, par exemple pour les corps de charrue. Après le montage, un contrôle de qualité est effectué avant que les machines ne soient livrées dans le monde entier.
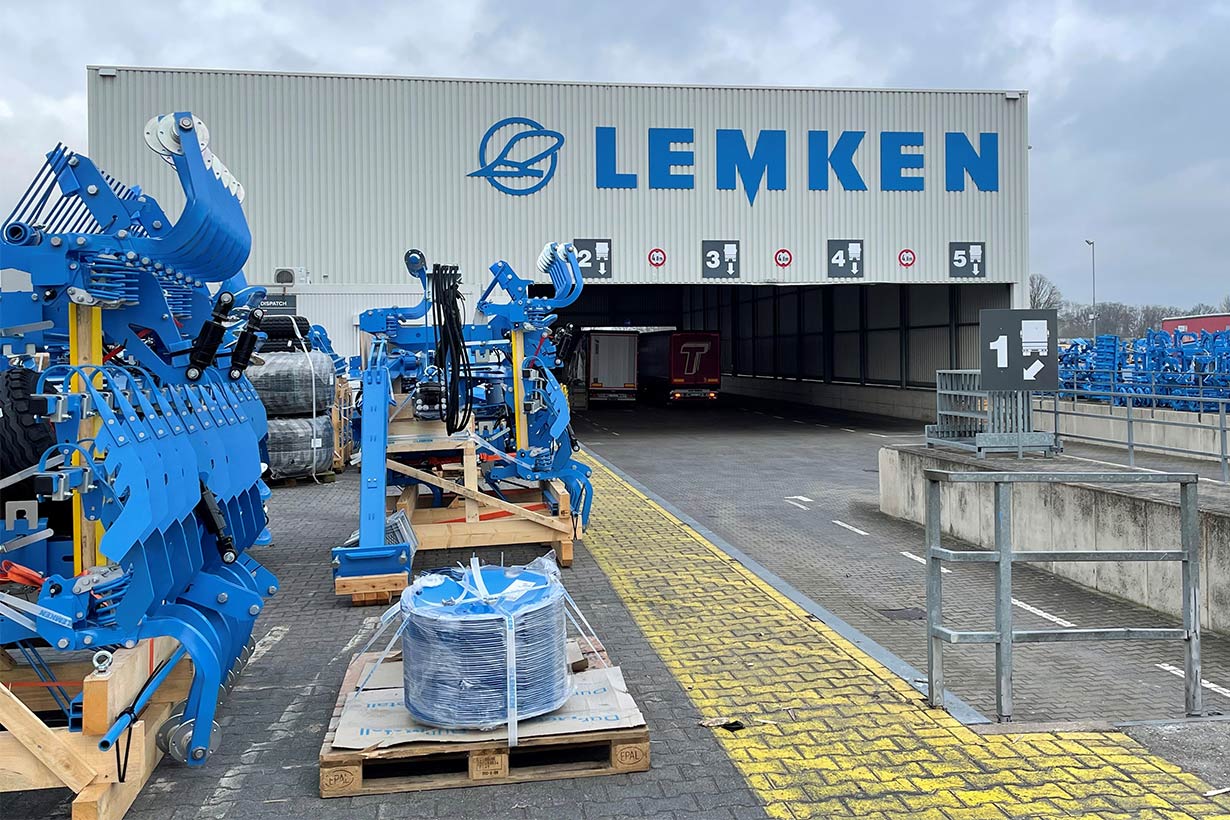
Aux heures de pointe, le service d'expédition charge jusqu'à 40 camions par jour en deux équipes. Cinq rampes de chargement permettent de charger simultanément cinq camions par chariot élévateur ou par grue. Parallèlement, environ 1.000 conteneurs sont expédiés chaque année pour l'outre-mer. LEMKEN a le statut d'opérateur économique agréé. Cela simplifie et accélère les formalités douanières, car les documents douaniers peuvent être établis sur place.
Notre usine à Alpen en film
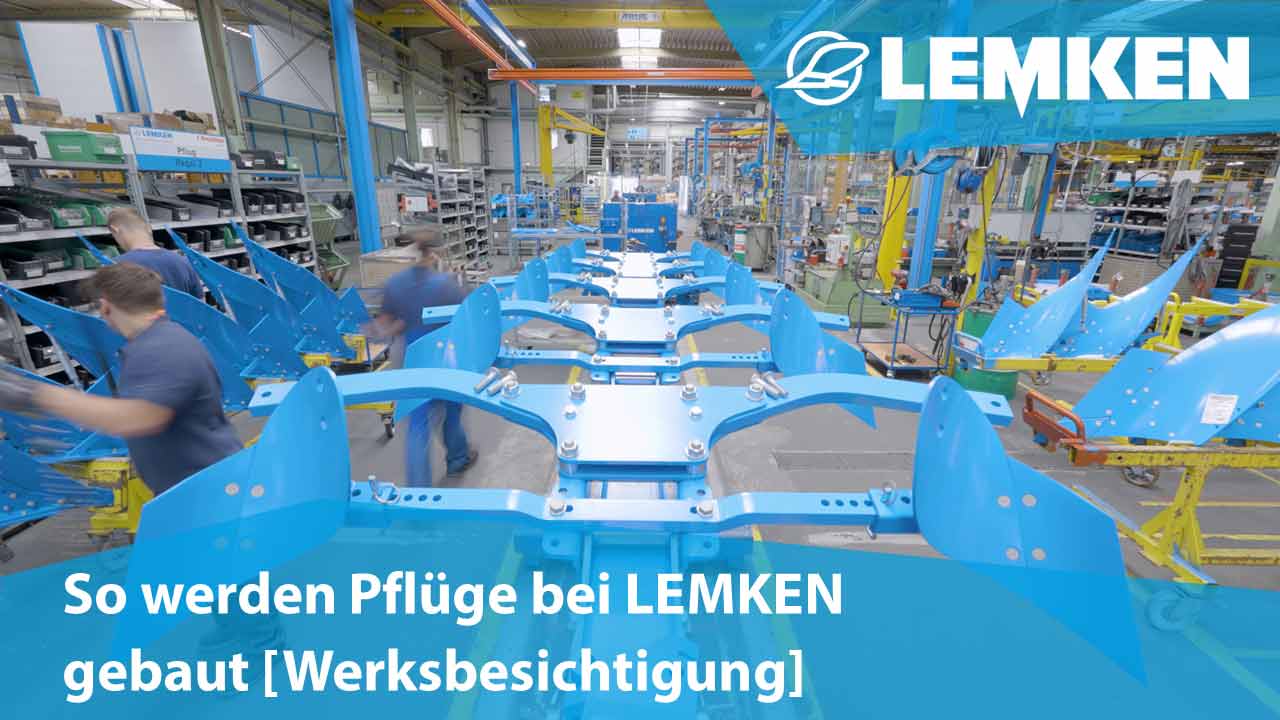
Vous êtes curieux de connaître les machines agricoles à Alpen ?
Notre personnel se fera un plaisir de vous faire visiter notre usine d'Alpen, du lundi au vendredi, le matin ou l'après-midi pour groupes d'un minimum de 15 et d'un maximum de 50 personnes.
Vous avez encore des questions ? Vous trouverez toutes les réponses en bref dans notre FAQ !
Nous nous réjouissons de votre visite !
FAQ pour l'usine LEMKEN à Alpen
Veuillez prévoir un total de 3 à 4 heures (avec repas) pour votre visite à Alpen.
Pour des raisons techniques, nous pouvons vous proposer de commencer la visite à 10h ou à 13h30. Des horaires différents sont éventuellement possibles après concertation.
Nous proposons la visite de l'usine d'Alpen à des groupes de 15 personnes minimum à 50 personnes maximum. Pour des raisons d'assurance, l'âge minimum des participants est de 14 ans.
Vous êtes un particulier ou un petit groupe intéressé par une visite ? Veuillez nous contacter du lundi au vendredi matin. Nous essaierons de vous permettre de participer à un groupe existant.
Pour des raisons techniques de production, notre usine d'Alpen n'est pas accessible aux personnes à mobilité réduite. Nous vous prions de bien vouloir comprendre que seules les personnes en bonne condition physique peuvent participer à la visite de l'usine sans avoir recours à des moyens auxiliaires tels qu'un déambulateur ou un fauteuil roulant.
L'usine est naturellement bruyante. Afin que vous puissiez suivre la visite sans restriction, nous vous équipons d'écouteurs sur place.
Après la visite de l'usine, vous aurez la possibilité de vous rendre dans notre FanShop. Vous pourrez y payer en espèces ou par carte EC. Veuillez indiquer directement lors de votre inscription si vous êtes intéressé par la visite de la boutique.
Vous pouvez également vous informer au préalable sur nos articles FanShop très appréciés :
Nous vous proposons une visite guidée gratuite de l'usine. Vous êtes cordialement invités à prendre un café et une boisson froide. Seule la restauration optionnelle est facturée au prix coûtant. Celle-ci doit être payée en espèces sur place.
Prix par personne
- Café/gâteau 6,50
- Pains garnis 8,00 €
- Déjeuner 17,00 €
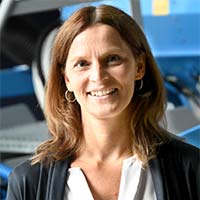
Kirsten Klancisar
Le marketing